Формирование покрытий из самофлюсующегося порошка на основе сталей аустенитного класса с добавлением молибдена
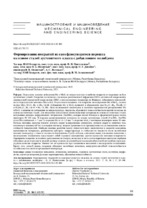
Authors
Date
2021Publisher
Another Title
Forming Coatings from Self-Fluxing Powder Based on Steels of Austenite Class Adding Molybdenum
Bibliographic entry
Формирование покрытий из самофлюсующегося порошка на основе сталей аустенитного класса с добавлением молибдена = Forming Coatings from Self-Fluxing Powder Based on Steels of Austenite Class Adding Molybdenum / Ф. И. Пантелеенко [и др.] // Наука и техника. – 2021. – № 2. – С. 95-100.
Abstract
Определено влияние добавления Мо и МоS2 на микроструктуру и свойства покрытия из порошков на базе аустенитных сталей. Покрытия исследовали с помощью рентгеновской дифракции (XRD), оптической микроскопии, сканирующей электронной микроскопии (SEM) с использованием твердомера по Виккерсу. Абразивную износостойкость определяли по методике Pin on disk. Результаты показывают, что покрытие, не содержащее Mo и МоS2, состоит из фаз (Fe), M7(C, B)3 и (Fe, Cr)2B. Добавление Mo и МоS2 приводит к образованию фаз M23(C, B)6, Mo2(B, C) и Fe3Mo3(C, B), где M = Fe, Cr, Mo. Цель исследований заключалась в изучении характеристик распределения Мо и МоS2 и влияния их добавления на микроструктуру, твердость, абразивную износостойкость покрытия из сплава на основе аустенитных сталей. Для напыления использовали композиционные материалы на основе аустенитных сталей, полученных методом диффузионного легирования (Aus0Mo), которые имеют близкую к сферической форму частиц диаметром 50–100 мкм. В порошок композиционного материала на основе аустенитных сталей (Aus3Mo, Aus5Mo и Aus7Mo) добавляли 3–7 мас. % порошка Мо и 1,0–1,5 мас. % порошка МоS2 с частицами диаметром менее 50 мкм. Методы наплавки, включая газовую дуговую сварку вольфрамовым электродом, дуговую сварку в защитном газе, плазменную наплавку (РТА) и лазерную наплавку, широко применяются в промышленности для повышения износостойкости поверхностей. Наиболее важные различия между этими методами заключаются в скорости осаждения, применимости материалов, разбавлении субстрата, микроструктуре и стабильности твердости после воздействия высоких температур, а также в стоимости изготовления. Среди методов, описанных выше, плазменное напыление с последующим оплавлением представляет собой хорошую альтернативу другим процессам наплавки поверхности. Перегревать покрытие до полного расплавления не следует, поскольку в этом случае первичные кристаллы карбидов и боридов хрома переходят в жидкий раствор и при последующей кристаллизации образуют более грубую структуру, ухудшая качество покрытия. Именно это не происходит при плазменном напылении с последующим оплавлением. Кроме того, способ дешев, покрытия обладают достойным качеством, конкурентоспособной износостойкостью и стабильностью свойств при высокой температуре.
Abstract in another language
The paper presents a study of the effect of adding Mo and MoS2 on the microstructure and properties of a powder coating based on austenitic steels. The coatings have been studied using X-ray diffraction (XRD), optical microscopy, scanning electron microscopy (SEM), a Vickers hardness tester, and abrasion wear resistance has been determined by the Pin on disk method. The results show that a coating that does not contain Mo and MoS2 consists of the phases (Fe), M7(C, B)3 and (Fe, Cr)2B. The addition of Mo and MoS2 leads to the formation of phases M23(C, B)6, Mo2(B, C) and Fe3Mo3(C, B), where M = Fe, Cr, Mo. The main goal of these studies was to study characteristics of Mo and MoS2 distribution and the effect of their addition on the microstructure, hardness, and abrasion wear resistance of an alloy coating based on austenitic steels. Composite materials based on austenitic steels obtained by diffusion alloying (Aus0Mo), which has a nearly spherical shape with a diameter of 50–100 μm, have been used for deposition. 3–7 wt. % of Mo powder and 1.0–1.5 wt. % of MoS2 powder with a diameter less than 50 μm have been added in the powder of the composite material based on austenitic steels (Aus3Mo, Aus5Mo, Aus7Mo). Surfacing methods, including gas arc welding with a tungsten electrode, arc welding in shielding gas, plasma surfacing (PTA) and laser surfacing are widely used in industry to increase wear resistance of surfaces. The most important differences between these methods are deposition rate, applicability of materials, substrate dilution, microstructure and hardness stability after exposure to high temperatures, as well as manufacturing cost. Among the methods described above, plasma spraying followed by fusion is a good alternative to other surfacing processes. The coating should not be overheated until it is completely melted, since in this case the primary crystals of chromium carbides and borides pass into a liquid solution and upon subsequent crystallization, form a coarser structure, worsening the quality of the coating. This is precisely what does not occur during plasma spraying followed by reflow; in addition, the method is cheap, coatings are of high quality, competitive wear resistance and high stability of properties at high temperature.
View/ Open
Collections
- № 2[12]